What are the Four Stages of Ground-Up Construction?
An organization has been scaling up over the last several years and increasing profits and staff but is quickly running out of room in the existing building. The company does not want to slow growth and needs a larger space to continue to expand. They have two options: renovating the existing structure or ground-up construction. Both options have pros and cons for the company. After assessing the real estate market, construction cost, financing options, and renovation limitations, the company decides to build a new space.
What is Ground-up Construction?
What is ground-up construction, and why would the company select this option for expansion?
Ground-up construction means constructing an entirely new space in a brand new location, while a renovation modifies an existing structure. This gives companies unlimited flexibility in materials and design, meaning it can be customized to meet the specific needs of the business better. A technology company will need larger conference rooms, robust electrical connections in all offices, and large storage areas, while a manufacturing company will need open floor areas, fewer offices, and massive storage and packing areas. Ground-up construction can accommodate these specific needs easily.
1. Ground-up Design?
The design process for ground-up development involves creating a project plan which includes construction drawing, utility connections, and workflow. Next, the designer creates schematic designs and researches materials. This process takes about four months for small projects and six months for large projects. Finally, because ground-up construction offers flexibility, each room is designed and assessed for function and utility. Designers combine natural light requirements, electrical connections, colors, materials, workspace flow, and overall aesthetic for each room.
During the design, the project owner evaluates it and ensures it meets building codes and regulations. Failure to meet building codes causes extensive delays and costs during the construction phase. The business will set up construction funding and loan options before the pre-construction phase.
2. Pre-Construction Phase
The pre-construction phase begins when the project owner tells the general contractor to start the project. The length of this phase will depend on the scope of the project and can range from two to twelve weeks. While twelve weeks may seem excessive, this phase is critical for the overall success of the build, meeting timelines, and budgets. The pre-construction phase includes material sourcing, subcontractor quotes, and building permit acquisition. A site inspection, which minimizes environmental risks, concludes this stage.
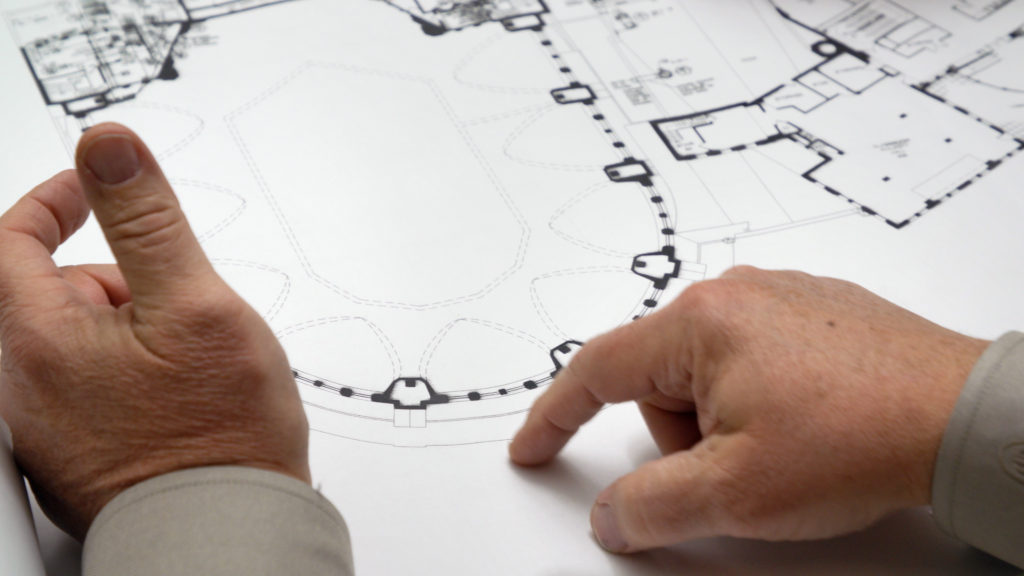
3. Construction
The construction phase covers all parts of the build. First, the construction team meets to determine site access, material storage, quality control, and work hours. This is the most active stage of the process because it includes groundbreaking, site excavation, foundation pouring, framing, interior and exterior work, roofing, and utility connection. Depending on the project size, this phase can take a few months or several years.
4. Post-Construction
Post-construction falls between construction completion and when the business moves into the building. Depending on the project, post-construction takes one to four weeks. This phase starts with extensive testing of the finished building by the project owner, designer, and general contractors. The final stage of post-construction is to obtain the certificate of substantial completion. After approving the project requirements, the business receives the certificate.
Benefits of Ground Up Construction
The most significant benefit of ground-up development is starting with a blank slate. From design to project planning to the construction process, companies have more creative freedom to create what they need. Companies can also meet many sustainability goals during ground-up construction by choosing sustainable materials, installing efficient lighting, installing environmentally friendly flooring and roofs, and taking advantage of natural ventilation. Sustainable materials require less energy consumption for growth, production, and transportation. The top sustainable materials for commercial buildings include bamboo, cork, reclaimed or recycled wood, metal, precast concrete slabs, and sheep’s wool insulation, according to Smart Cities Dive. Locally sourced materials also reduce transportation costs during building projects.
Ground-up Construction with Kroeschell
Building a new commercial property takes investment and planning. The key to success with construction projects is understanding the process and planning appropriately. Involving a reputable company in the initial planning stages can save time, construction funds, and stress.
At Kroeshell, we’ve committed to supporting our clients during every phase of their ground-up construction project. For an amazing experience in ground-up development, schedule a call with Kroeschell.